Unleashing the power of connected Assets
Empowering businesses with real-time visibility and control of their assets.
Designed for demanding industries like mining, logistics, and energy, our customizable solutions transform operational data into strategic insights, maximizing uptime, safety, and efficiency at every level of operation.
Why Leading Companies Trust Us
Our proven track record speaks for itself. Here are the key numbers that demonstrate why businesses worldwide choose our solutions to solve their transportation challenges and improve operational efficiency.
Units Sold
Our trusted solutions are relied upon by companies worldwide.
Countries
With deployments in over 14 countries, our technology is trusted by leading companies worldwide
Monthly Server Traffic
An average of 209GB of data transmitted to our servers each month, supporting the operations of top enterprises.
Billion Data Points Processed
Highlighting the strength of our data processing performance.
Dragonfly
"One Device to Connect Them All"
Easily connect all your diverse business assets, regardless of interfaces or protocols. Experience uninterrupted connectivity with 4G/LTE, WiFi, BT or Ethernet. Maximize your capabilities with seamless integration and enhanced programming flexibility through the embedded eFlow Manager. With the added integrated battery and supercapacitors, you’ll never miss a bit.
Powered by an industrial grade Qualcomm processor, Dragonfly runs emd-OS, an ultra-secure operating system based on a customized and hardened Linux kernel.
Optimized for exceptional speed, reliability, and security, emd-OS features Secure Boot technology along with dedicated cryptographic hardware to deliver intrinsic protection at every layer. Extensively penetration-tested by industry-leading cybersecurity firms, our operating system is fully auditable, empowering our clients to verify its security independently. Unlike hardware from other manufacturers that may include concealed backdoors embedded by controversial foreign entities, Dragonfly replaces all embedded component firmware with fully transparent software developed exclusively by emd and validated through rigorous client audits.
Asset Management Platform
Designed to meet our clients needs, the emd-cloud platform brings together all our services into a single, seamless experience.
With just one login, you gain centralized control over your entire ecosystem of connected devices. Easily access:
- Remote device configuration: Adjust and manage connectivity settings, interfaces, and system parameters from anywhere.
- Firmware updates: Deploy individual or batch updates effortlessly to keep all devices running on the latest versions.
- eFlow programming: Develop, modify, and deploy automation rules directly on your devices for optimized operations.
- Device health monitoring: Track critical metrics like connectivity status, battery levels, processor usage, memory consumption, and more.
Beyond management, our platform also provides real-time device data and CAN logs, allowing for in-depth performance analysis, troubleshooting, and predictive maintenance. Whether optimizing a single asset or overseeing an entire fleet, emd-cloud empowers you with the insights and tools needed for smarter, data-driven decision-making.
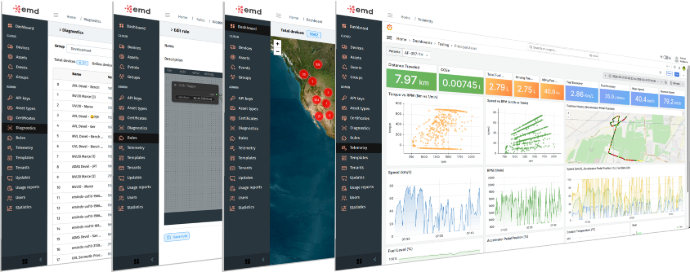
Asset Management
Provision, Update, and Monitor at one click. Monitor the health status of all your devices, including connectivity, battery, bus, signal strength, CPU usage, free memory, and more. View firmware versions and perform individual or batch updates. Easily modify device configurations such as APN, Wi-Fi, Ethernet, CAN, Modbus, and more.
Advance CAN Logging
This feature enables precise data analysis by triggering CAN logs when the bus meets pre-configured filter conditions, ideal for troubleshooting specific issues. You can also perform large-scale CAN logging to monitor engine performance or diagnose potential problems.
Dashboard
Using Grafana, we offer fully customizable dashboards to meet each customer's specific needs. You can integrate various data inputs such as CAN bus telemetry, GPS information, GPIO, and more, allowing you to create tailored, insightful dashboards.
Event Monitoring
An interface that allows you to view predefined events such as alarms or info from your devices. You can also create custom events by configuring them through our eFlow Manager system.
eFlow Edge Computing
Deploy and manage your applications within our platform using the Edge Rule Engine. This allows you to build and execute IoT business logic directly on edge devices, enabling you to process data on your private cloud or visualize it through the emd Cloud platform.
GraphQL API
Through our API you can integrate different device information directly to your application.
DAQ
Allows clients to upload their own custom DBC tables, which define how to decode CAN parameters. These tables often contain proprietary information crucial for accurate monitoring and diagnostics. By enabling clients to use their own tables, we mitigate the risk of data leaks involving sensitive information, thereby ensuring enhanced security and fostering trust in our system.
Remote Technician Suite
Stream real-time CAN data directly to your browser via a low-latency P2P tunnel, and perform on-the-fly conversions using DBC templates to monitor live vehicle operations. This also allows customers to remotely access the vehicle's J1939 network with RP1210-compliant OEM software, enabling remote diagnostics and repairs without the need to send a technician on-site.
Virtual Sensors
Generate new inferred data measurements by combining the information available through different interfaces (such as CAN, MODBUS, etc.) and the equipment’s sensors. For example, it is possible to estimate the approximate weight transported by a truck, the Total Fuel Used (TFU), or various hour meter metrics, such as driving time, brake usage, engine brake usage, and more.